Commercial
Commercial Air Conditioning Solutions for Your Business Needs
Need reliable installations and tailored maintenance plans? Contact us for a free quote and discover the perfect solution for your business today!
Refrigeration
Complete Commercial Refrigeration Solutions
From installations to maintenance and repairs, we’ve got it all. Contact us for a free quote and see how our professional service takes your business to the next level!
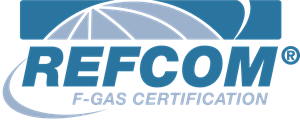